Dissertation
CEVIAN-ORI
Since ancient times in Kyoto prefecture, the city of Ayabe has held a long tradition of highly skilled weavers; its history in thread and textile craftsmanship has made it home to one of Japan's leading fabric companies, and an original paper cloth, known as CEVIAN-ORI.
Category: | Material |
---|
Date: | 2020.03.24 |
---|
Tags: | #cevianori #visvim |
---|
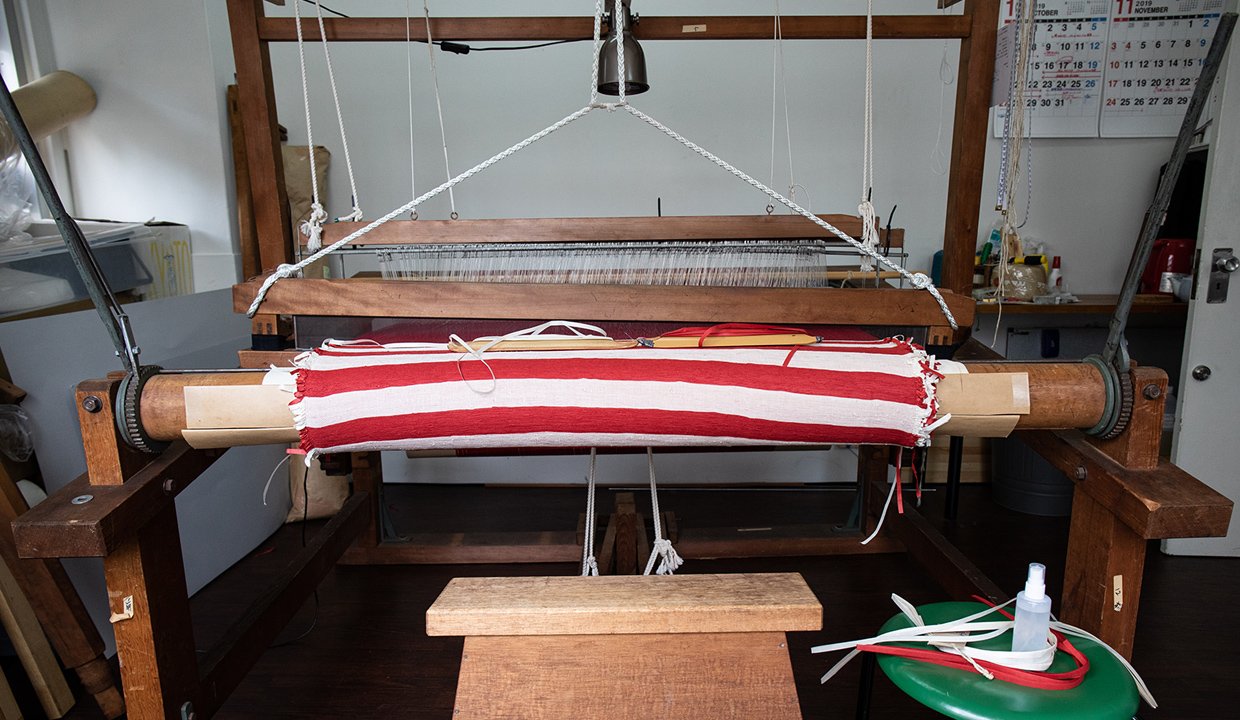
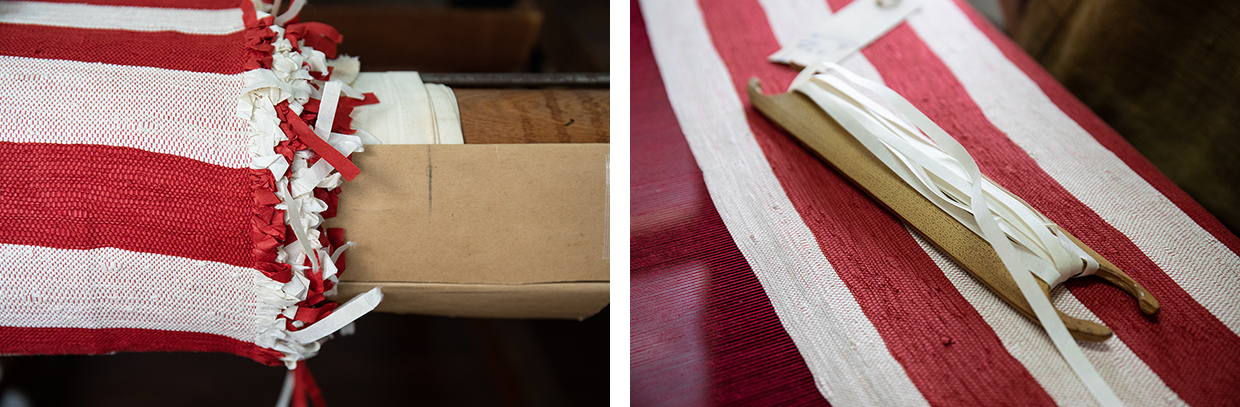
Since ancient times in Kyoto prefecture, the city of Ayabe has held a long tradition of highly skilled weavers; its history in thread and textile craftsmanship has made it home to one of Japan's leading fabric companies, and an original paper cloth, known as CEVIAN-ORI.
In 1976, a former employee of Gunze, Keiji Umehara developed this fabric while studying yarns and combining another traditional craft from northern Ayabe, Kurotani Washi; weaving the Japanese paper as a weft yarn. The texture and appearance, and thus name, pays homage to the beauty of the Yuragawa river's currents which flow through the city. Originally, Umehara had been inspired to use Kurotani paper, upon discovering archives dated 700 years ago about the town's Ankokuji Temple, noting the documents had hardly deteriorated whilst maintaining its glossy finish peculiar to washi. Through repeated experimentation, Kurotani Washi was incorporated as a thread, woven manually into a fabric; inventing not only a eye-catching texture, but also a lasting, highly durable and anti-bacterial fabric with highly-breathable properties.
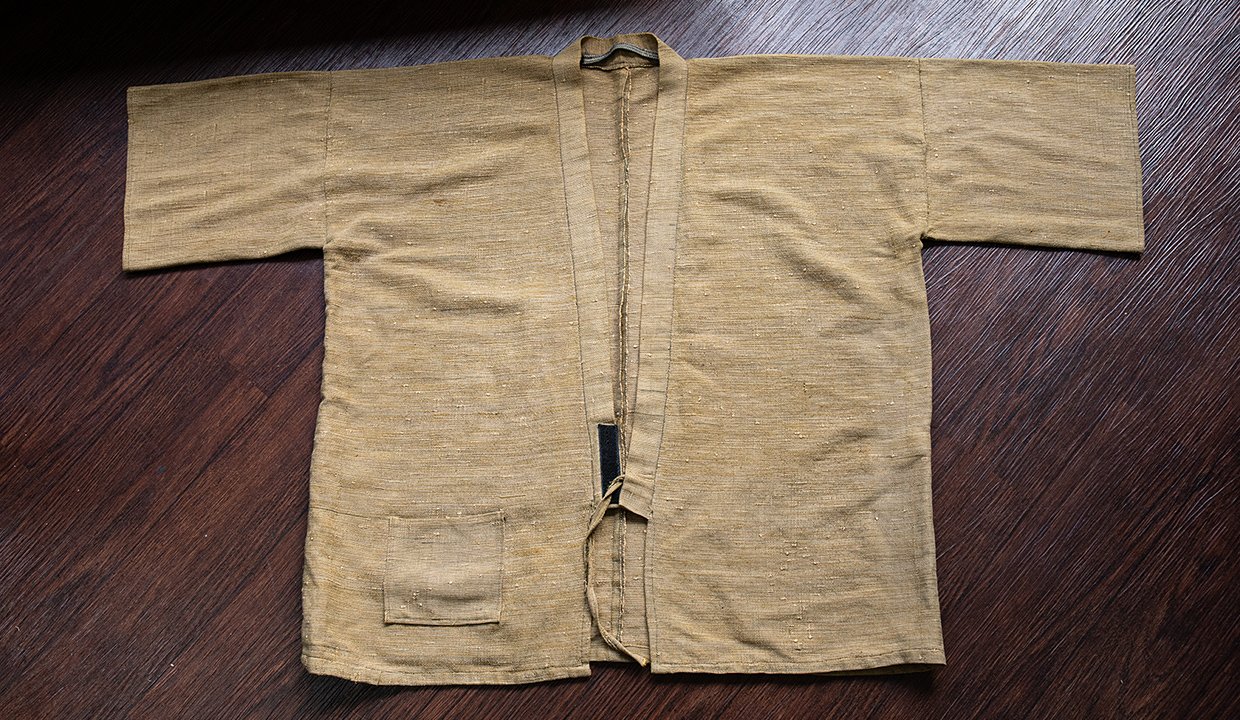
Almost 50 years later, texture of CEVIAN-ORI remains mainly unchanged. Yuji Asada, grandson of Umehara, now inherits the craft expertise, and he aims to share the beauty of CEVIAN-ORI to a wider audience.
The process for weaving the textile takes a considerably long time; great care and skill is required as not to tear the delicate Japanese paper. (The impressively low daily production average is about 8cm per hour or 60cm per day.) Attempts at increasing the productivity via use of mechanical power have failed to replicate the same texture finish, as the washi yarns are often cut and finished poorly.
Furthermore, the dedicated time and effort by hand adds an attractive unevenness and durability to the fabric, which can even practically be washed in the same way as cotton cloth.
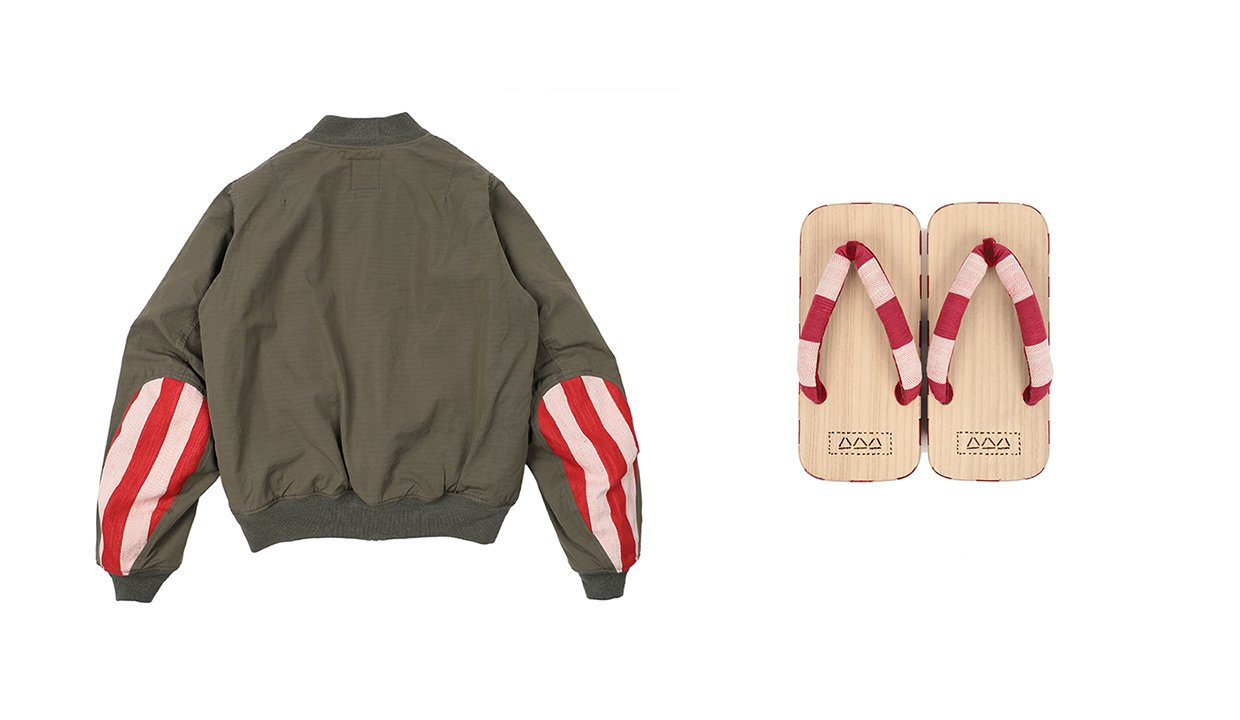
Learning from and making use of original and reliable age-old craftsmanship skills, we are able to create new things by also innovating a combination of these ideas and techniques. Traditional craftsmanship being incorporated into modern product development shouldn't be considered superior simply due to its history, but rather, appreciating the interesting and well-considered approaches that create uniquely rich and timeless beauty in products.