Dissertation
Aizome (Natural Indigo Dyeing)
Indigo dyeing, known in Japan as "aizome", is one of the most indicative forms of natural dyeing and has a history of being practiced all over the world since ancient times. Similar to other plant or vegetable-based dyes where the pigment comes from plants, so too does the indigo pigment, which is sourced naturally from Japanese Indigo (Persicaria tinctoria) as well as other plants. However, the process to create the dye itself is vastly different in comparison.
Category: | Processing |
---|
Date: | 2022.06.07 |
---|
Tags: | #aizome #indigo #indigocampingtrailer #naturalindigo #ss22 #visvim |
---|
Indigo dyeing, known in Japan as "aizome", is one of the most indicative forms of natural dyeing and has a history of being practiced all over the world since ancient times. Similar to other plant or vegetable-based dyes where the pigment comes from plants, so too does the indigo pigment, which is sourced naturally from Japanese Indigo (Persicaria tinctoria) as well as other plants. However, the process to create the dye itself is vastly different in comparison.
Whereas most plant dyes are created by steeping plant material in hot water to extract water-soluble pigments, the pigment for the indigo color is insoluble. Due to this, it is necessary to perform alkaline reduction in order to dissolve the pigment and extract the dye. This special process required in aizome is known as "ai-date" in Japan.
There are two major ai-date methods: "hakkō-date", a natural method which uses fermentation bacteria, and "kagaku-date", a scientific method which uses a reducing agent. Both methods follow the same logic of fermenting the leaves of Japanese indigo plants along with other raw materials to produce an indigo pigment to be used as a dye which turns an indigo blue color following oxidization. Each method however produces noticeably different results in the final product both in terms of color and the quality of the finish.
"What I'm aiming for is the indigo color of the Edo Period. It's characterized by its richness and transparency. It's a deep indigo that feels as if it's made up of a series of layers of clear, transparent colors; rich but fresh, without any murkiness to it," Tokuyuki Murata tells us, a craftsman at the indigo-dyeing workshop Kosōen in Ome, Tokyo--a workshop that has dyed a number of products for us at visvim. Murata has held a tenacious fastidiousness towards indigo dyes for many years. He tells us, laughing, "I think I have almost done as much trial and error as is possible," but all the same, he continues his research on getting ever closer to the color he's aiming for, using techniques established in the Edo Period where the fermentation method and dyeing method affect the final finish.
Hakkō-date, which has been practiced since the Edo period and beyond in Japan, begins with the drying of the leaves of the Japanese Indigo plant, which are then fermented in order to produce a substance called sukumo--the base for indigo dye. Next, lye (made from a mixture of wood ashes), alcohol, wheat gluten, and lime are added to the sukumo and it is left to rest. The mixture needs to be stirred in the morning and evening where after three or four days the fermentation process will have begun, at which point more lime is added in. When the fermentation has sufficiently progressed, more lye is added then the rim of the vats are raised. After one week to ten days, it will finally be ready to be used as a dye.
This is a simplified explanation of the hakkō-date process, but there are no fixed rules in how to ferment the mixture or what ingredients to use--this includes the origin of the sukumo, what type of ash is used, the concentration of the lye, the amounts of the other ingredients, or even the time required for each step of the process. What makes the process interesting is that the dyers and craftspeople will use their extensive knowledge and experience to adjust any of these factors to create the color they aim to achieve. It goes without saying that this process allows for a greater freedom of expression than kagaku-date, which requires specific chemicals all the time. However, the adjustments and oversight required during the fermentation steps make it a more laborious process in general.
"The fermentation of the indigo dye isn't something that takes a specified amount of time--you need to keep an eye on the progression of the fermentation as you prepare to use the dye," says Murata. "Not only that, you need to manage that state so that it can be maintained for as long as possible. The quality of the ash is crucial for that reason. Some people even go as far to say that the ash is what determines the color."
Before beginning the ai-date process of creating the indigo dye, you first need to prepare the lye. Commonly used ashes are from the Japanese blue oak, Japanese zelkova, or sawtooth oak. They need to be stored carefully to avoid oxidization. After judging the condition of each type of ash, they are then combined, and boiling water is added. Once the mixture has cooled, the supernatant lye is separated and stored. Then more hot water is added and the process is repeated again. This process is conducted four times in total over the course of approximately a week, resulting in four different solutions of lye with differing alkaline concentrations. These are then picked and used depending on how the fermentation of the dye is progressing. With high-quality lye, the indigo will ferment well, which results in not only a good color but also a stable and easily managed indigo dye.
"In particular, when dyeing something like shoes, the task becomes difficult unless the indigo has fermented really well," Murata tells us. "Not only are mixed materials used--such as canvas, leather, and rubber--each finished product has its own individual differences in its shape. They are sewn and assembled by hand, so oils and the like from the body can often stick on the material, causing difficulties for the dye. There are times when I hold my head in despair, but I have a desire to dye these difficult items well, too. This thought allows me to keep trying different things."
Combining the natural splendor of indigo dye with modern manufacturing techniques, we have experimented in various ways and wish to continue to create new innovative products. Continuing a process of trial and error alongside craftspeople, we hope that the fruits of our labor will be revealed in the products we make.
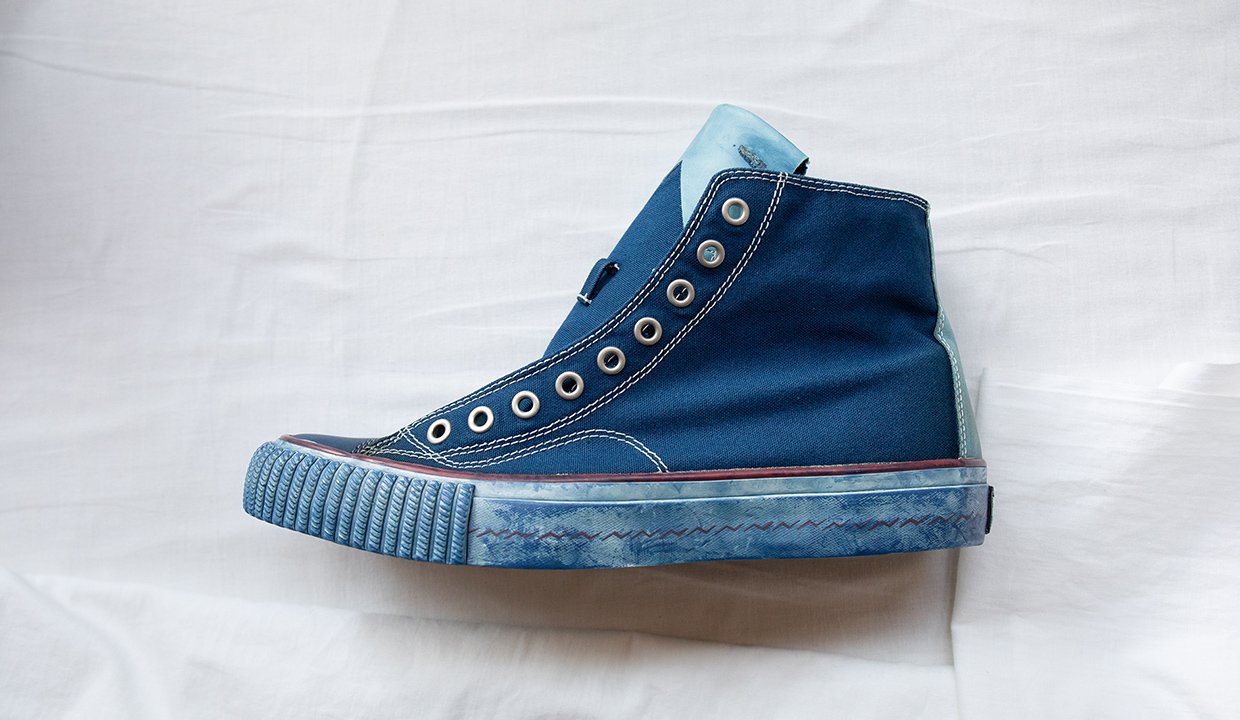