Dissertation
Doro-Zome (Mud-Dyeing)
Oshimatsumugi (Doro-Oshima) is widely known as a luxury silk fabric and traditional craft of Amami Oshima in Kagoshima prefecture. That sharp glamorous dark brown color is realized from the use of plants native to Amami and the doro-zome dyeing process where the yarns get soaked in mud.
Category: | Processing |
---|
Date: | 2022.02.01 |
---|
Tags: | #dorozome #muddyeing #ss22 #visvim.amami |
---|
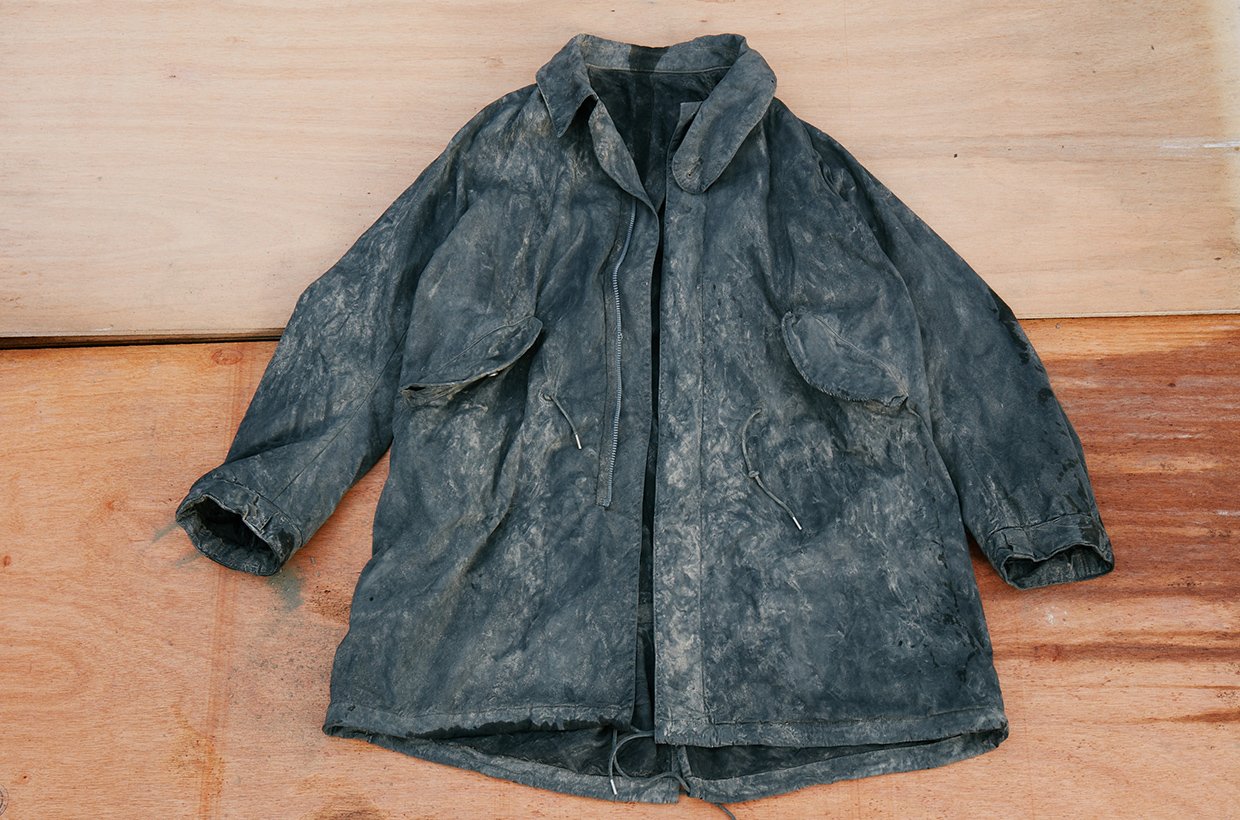
This coat is undergoing the mud dye process. It has been dried following the initial mud dye step in the process.
Oshimatsumugi (Doro-Oshima) is widely known as a luxury silk fabric and traditional craft of Amami Oshima in Kagoshima prefecture. That sharp glamorous dark brown color is realized from the use of plants native to Amami and the doro-zome dyeing process where the yarns get soaked in mud.
There is a chemical reaction which occurs between iron found within the mud in the fields and a tannic acid from the pigment of Sharinbai (Rhaphiolepis umbellate), a plant species of the Rosaceae tree also known as, Teechiki in the local Amami dialect, where fibers of silk and cotton transform into a deep black tone after being dyed repeatedly. This dyeing technique was believed to be in use already during the Mid-Edo Period and was said to have been discovered by chance when someone left (or perhaps hid) a vegetable-dyed (kusaki-zome) kimono in a rice field which they collected later to find a kimono that had dyed itself into a beautiful black color.
The fields of mud required for mud dyeing can only be readied in very limited areas of the land where the soil quality remains very fine but also must include an abundance of iron. Since ancient times Amami Oshima has had a distribution of mud from clay formations which include great amounts of iron, and these mud fields are found along the skirts of the mountain where they can absorb and retain mineral rich water that is runoff from upstream when it rains.
The largest field of mud on the island is maintained on the grounds of the Authentic Amami Oshimatsumugi Mud Dyeing Park in the Naze area of Amami city. There is a workshop surrounded by nature under blue skies where visvim has utilized the mud dye process from over 10 years ago under the stewardship of master dyer Mr. Nozaki.
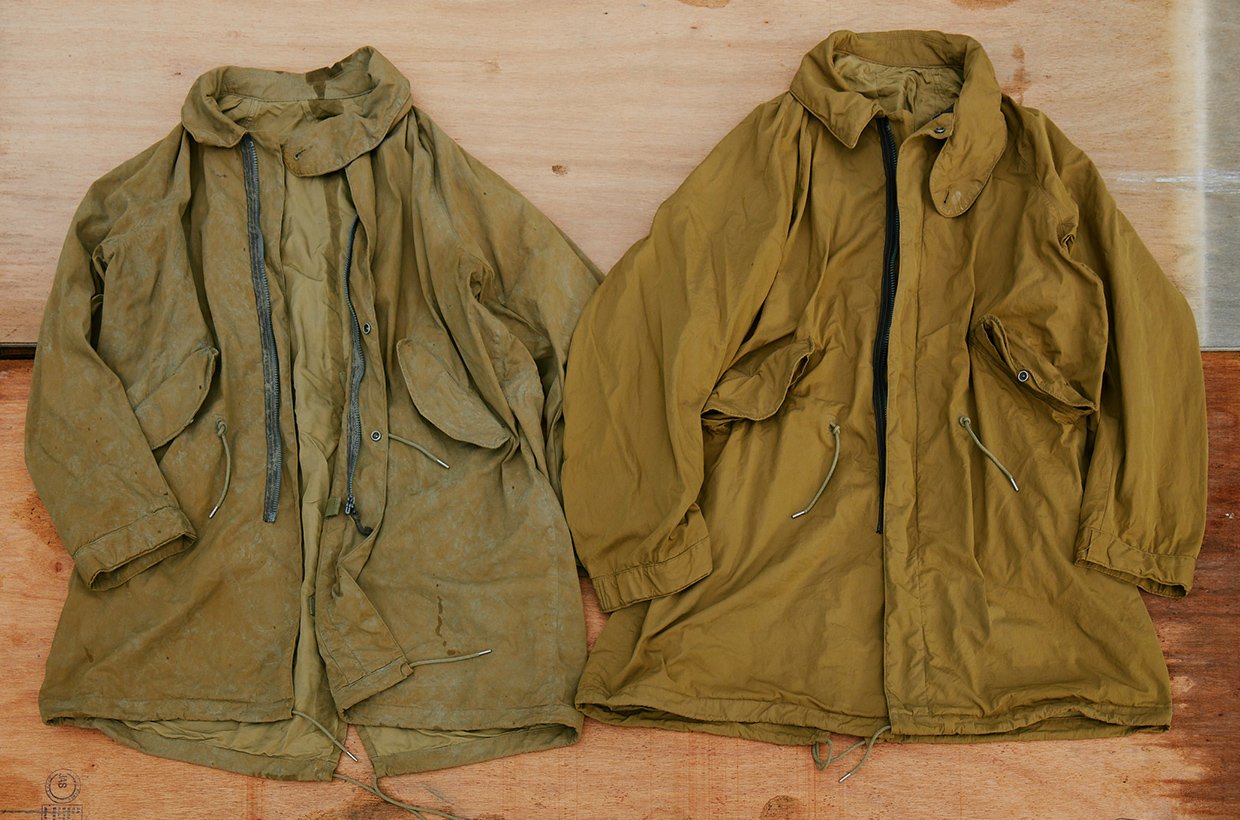
This coat is undergoing the next steps in the mud dye process. The coat on the left has been dried following the mud dyeing. The coat on the right has been washed after being hang dried.
"I feel a distinct charm that has an innate human touch by using an organic technique such as mud dyeing which makes use of the natural surroundings to create something so unique and uneven with such texture," says Hiroki Nakamura. "I wondered if I could create product that possesses a warmth and human touch by expanding the possibilities of such a technique and testing its application not only with natural fibers but also synthetic fibers. I continue to explore further development by taking the mud dye technique and creating new treatments and uses."
The clothesline area of the workshop is lined with dozens of jackets that have been dyed in the mud fields. Generally, the mud dye technique is applied to yarns, but in contrast to that, mud dyeing a finished garment creates a unique feeling where the texture is evident within the entire product rather than just the cloth or fabric itself.
The weight on a jacket that absorbs water from the surprisingly fine and viscous feeling mud is really something substantial. The craftsman stands knee deep in the mud fields carefully soaking each piece one at a time. Once a piece is hang dried the next step is the washing process. Maching washing is avoided to prevent any damage to the fabric or metal parts and a handheld tawashi brush is used to scrub away any excess. A repeat of these steps throughout the process further enhances the depth and increases character. By taking advantage of a technique that uses gifts of nature still around since ancient times, we provide a distinct new charm to modern materials.
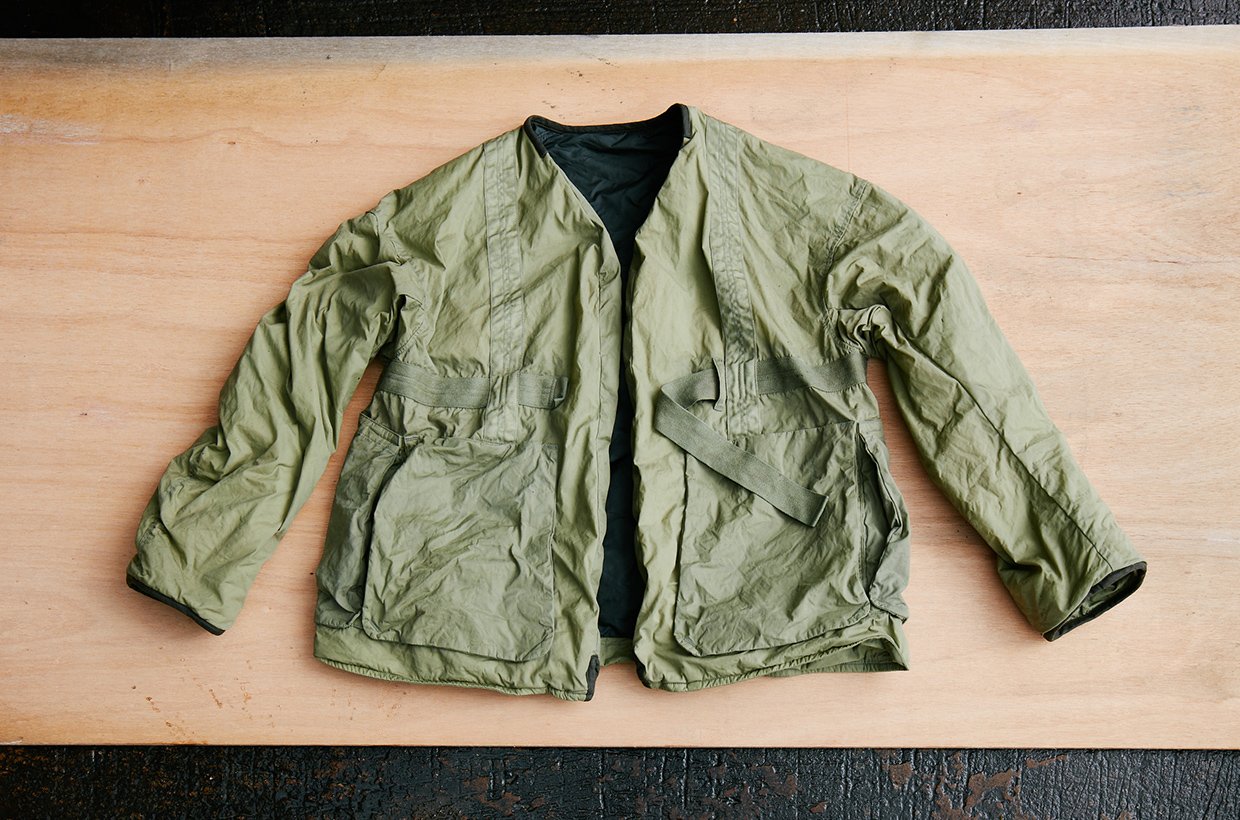
This coat has completed the finishing process. The piece has gone through the cycle of mud dyeing, followed by hang drying, and washing several times over.
Text: Kosuke Ide
Photo, Movie: Keisuke Fukamizu
Movie edit: cubism