Dissertation
Kurume Kasuri
"Kasuri" is a weaving technique that is characterized by its faint fragmented patterns: the threads are partially dyed beforehand and when woven together, the undyed segments of the thread appear as patterns on the fabric.
Category: | Material |
---|
Date: | 2023.01.10 |
---|
Tags: | #kurumekasuri #ss22 #visvim |
---|
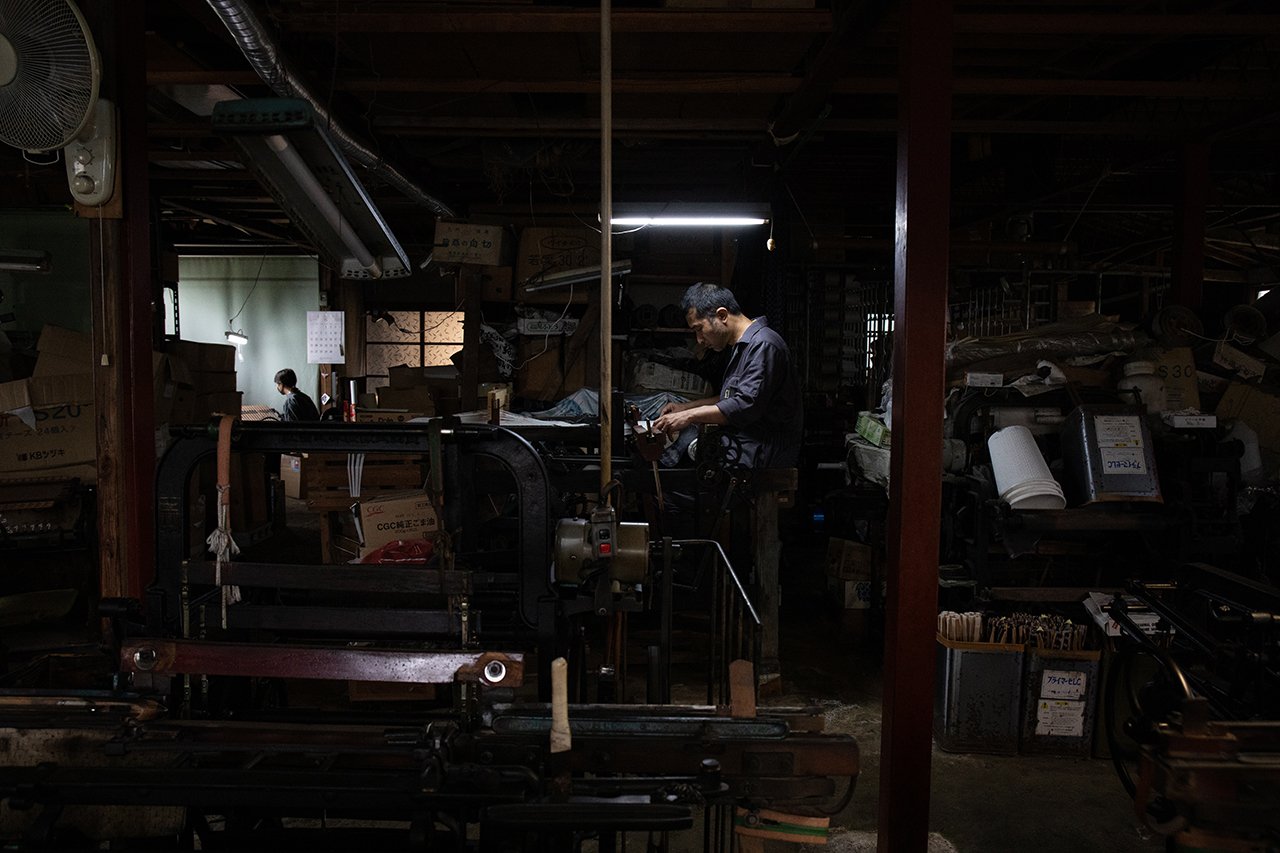
Movie, Photo: cubism
A unique style of kasuri, born in Kurume.
"Kasuri" is a weaving technique that is characterized by its faint fragmented patterns: the threads are partially dyed beforehand and when woven together, the undyed segments of the thread appear as patterns on the fabric. The technique is said to have originated in ancient India and came to Japan through China and the Ryukyu Kingdom. However, the kasuri style developed in the Chikugo region of southern Fukuoka, known as "Kurume Kasuri", has its own unique and independent history.
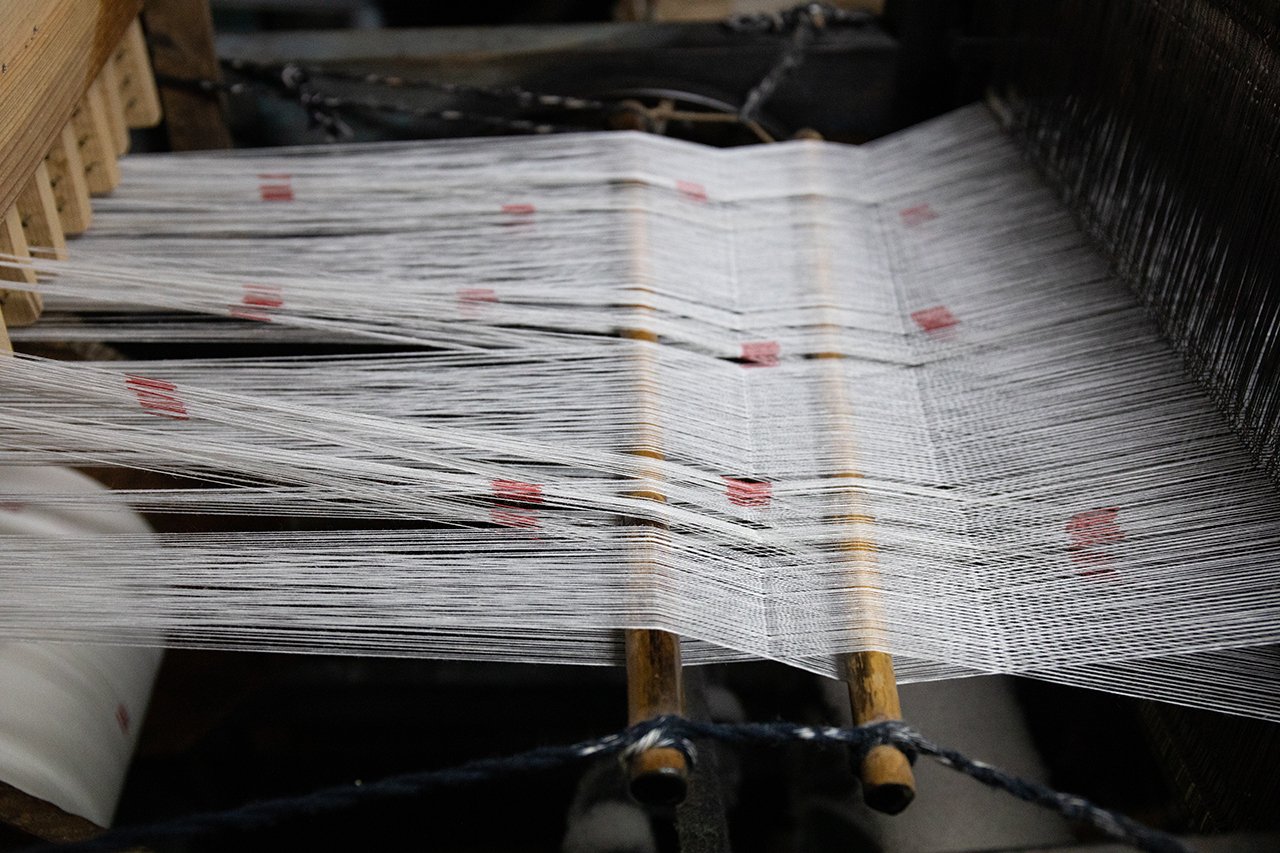
It was the 13-year-old daughter of a rice merchant who lived in Kurume Domain (present day Fukuoka Prefecture) known as Den (later married and became known as Den Inoue) whose contributions gave birth to the Kurume Kasuri technique during the late Edo Period (around 1800). Den had been a weaver since a young age, and it is said that she had the idea to create patterns in fabric by dyeing only certain specific parts of the thread when she saw white specks that had appeared on some old, faded indigo-dyed clothes. After a period of trial and error, she developed a technique wherein you protect the white thread from the dye by wrapping extra thread around it. After the dyeing process, the thread is unwrapped and when it is woven these undyed segments form patterns. Indigo-dyed clothes were used for everyday wear or for work and so their functionality was regarded above all else, which resulted in most of these clothes being plain. However, the patterned textiles Den created soon became hugely popular and were called "O-Den Kasuri" after her. Den dedicated her entire life to textiles and had taken on hundreds of disciples until her death at the age of 82.
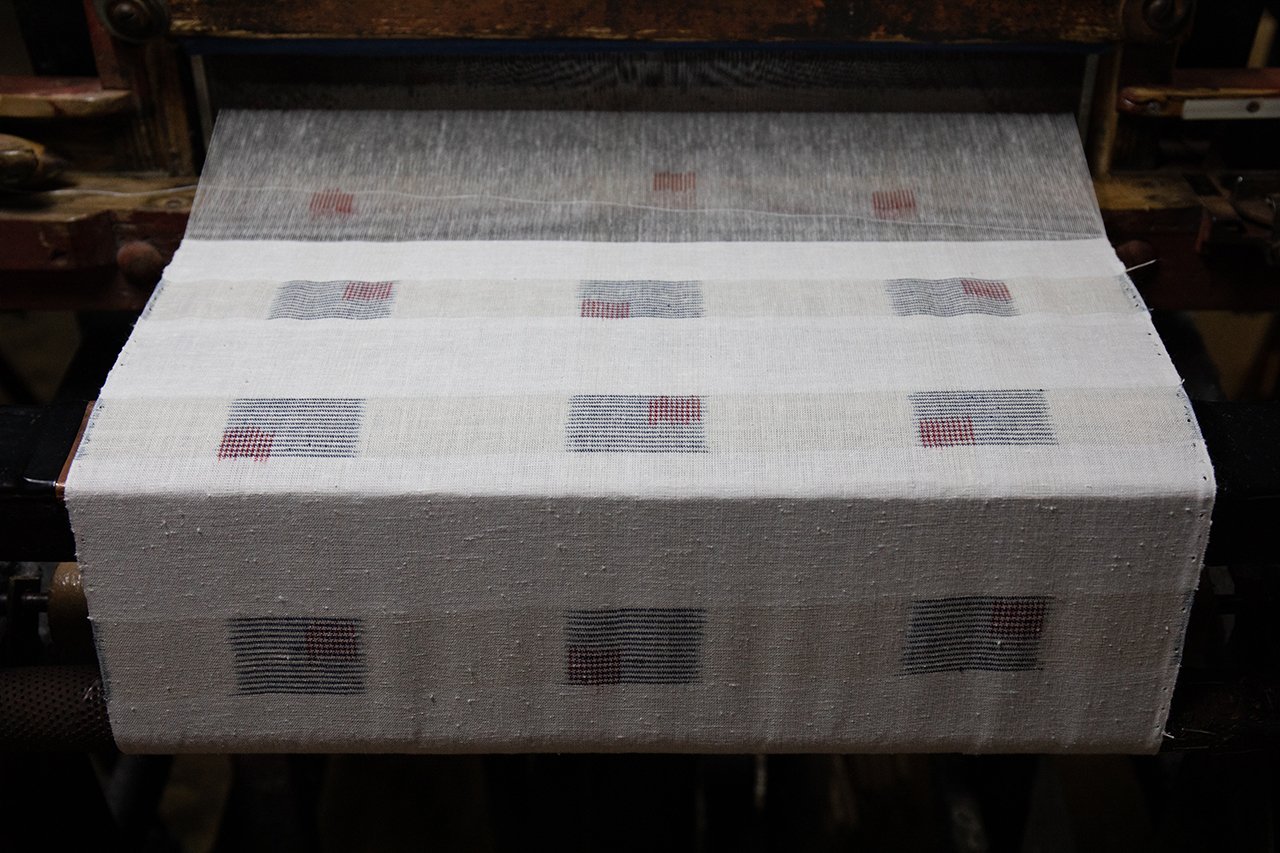
Photo: cubism
Kurume Domain promoted the production of Kurume Kasuri, and during the transition into the 20th century, these textiles were considered luxury goods. Two to three million pieces of Kurume Kasuri textiles were produced annually during its heyday. However, output severely decreased after World War II due to the ensuing modernization and move towards Western clothing, and now approximately only 70,000 pieces are produced per year. Despite this, compared to the current small scale of the two other styles that make up "Japan's Three Great Kasuri"--Bingo Kasuri in Hiroshima and Okayama, and Iyo Kasuri in Ehime--it can be said that Kurume Kasuri is still being produced with stable demand.
The distinguishing characteristic of Kurume Kasuri is its patterns that are created through selective dyeing. By tying extra threads around the thread used for the weaving, you can protect parts of the thread from the dye. This will cause the knotted areas to remain white, and when these threads are woven together as warp and weft, the white areas will form a pattern. Thanks to the natural shuffling up of the threads, unique, disjointed designs will begin to show themselves as the threads continue being weaved.
The practice of tying the protective extra threads is known as "kukuri", and when done by hand known as "te-kukuri". In the areas where Kurume Kasuri is currently being produced, there are weavers who instill an artistic practice into their work by both weaving and tying the threads by hand, but the practice of using a loom to complete both of these steps has been going on for almost a century and continues to this day.
In the Hirokawa district of Yame within Fukuoka Prefecture, Tomihisa Orimono--the Kurume Kasuri workshop which has worked on a number of products for visvim--is one of the few places where they weave both by hand and by machine. The fourth-generation head, Hiroshi Tomihisa, is a craftsman who conducts the entire process of creating these textiles himself--from the weaving to the indigo dyeing. In the workshop itself, a number of automated looms which have been used for almost a century line the walls. As they work, the periodic sound of clunking fills the room. Tomihisa always keeps his ears open for any changes to these sounds to ensure the looms are running without any issues.
"The temperature and humidity of the day can affect the condition of the looms," Tomihisa tells us. "I grew up with the noise of the workshop always in the background, so all I need are my ears to know how they're doing. When I was growing up there was also a workshop near my elementary school too, the whole town was full of these sounds."
Even with a machine, it isn't an easy feat to pair together the patterns on the warp and weft threads. You need to constantly be making minor adjustments to the machine by hand to fix the discrepancies that occur as you weave. In this way, the process is realistically half-automated and half-manual, requiring a high level of aptitude from the artisan no matter how the textile is woven.
Producing Kurume Kasuri is an incredibly intricate process, requiring around thirty steps to produce one piece of fabric. You first need to decide upon a design that takes into consideration the idiosyncrasies of the springiness of the thread and of the kasuri-ito, and then create a blueprint after calculating the placement of the warp and weft threads, the ji-ito (plain, monochrome thread), and the kasuri-ito (partially dyed, multicolored thread). Even these preparatory stages are incredibly complicated and require a lot of experience and expertise.
The thread must be soaked in hot water for a number of hours in order to rid it of any impurities and then starched, before moving onto the kukuri process where you tie hemp twine around the threads. The machines that do the work are old ones that have been modified by the artisans to be controlled by a computer. However, someone still must be constantly on watch in case of any unexpected occurrences, such as threads breaking.
After the kukuri process has been completed, the threads are reeled into skeins and are now ready to be indigo dyed. Tomihisa submerges sticks of bamboo with the skeins inside into a mix of vats with varying strengths of dye before wringing them out. As soon as they are wrung out, they are struck upon the ground numerous times in order to expose the thread to oxygen. The wet skeins get rather heavy, so this is a particularly arduous job.
Once the dyeing process is complete, the threads are starched again before they are individually spooled then rolled up to be used as warp or weft thread. A keen attention to detail is required at this stage too so the designs do not end up shifting. After all these detailed steps, the threads are finally ready to be woven.

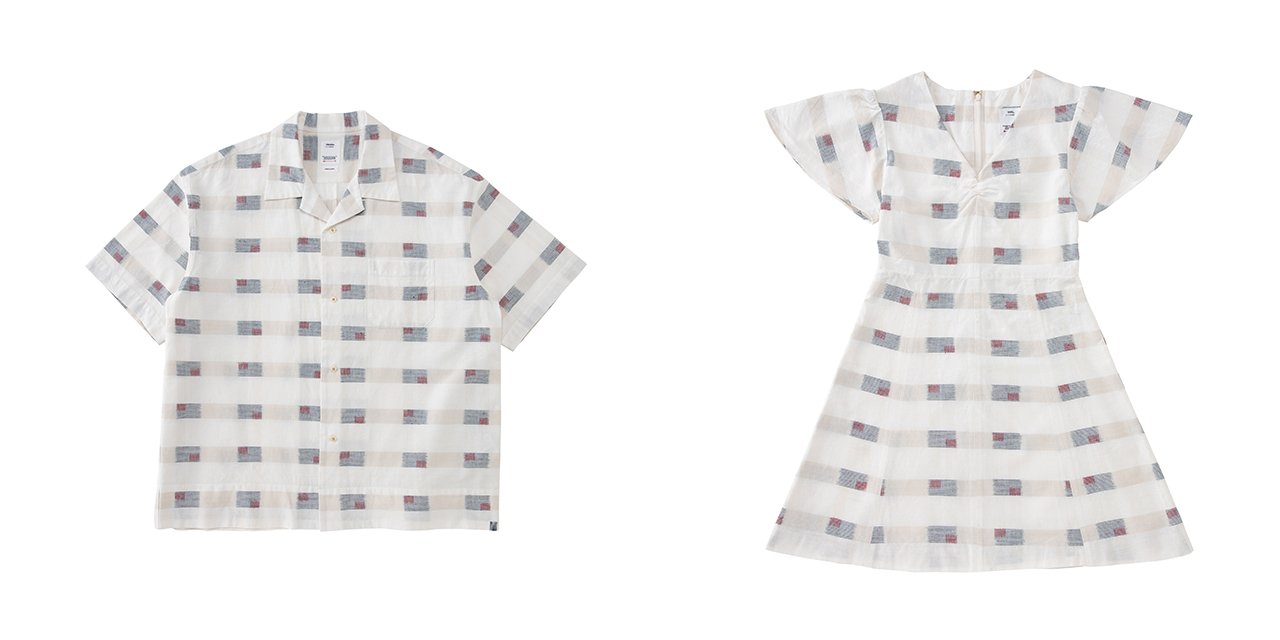
"The irregularities and the bleeding of the kasuri patterns creates a very unevenness to the fabric that is very organic in character. The differences in the cultures and history of kasuri depending on its country of origin and region are truly fascinating. I think it's incredible how over its long history it has fostered such sophisticated techniques," says Hiroki Nakamura, speaking of the appeal of Kurume Kasuri. "I would like to continue using these traditional techniques while creating a new, modern product, maybe by mixing linen with cotton in order to create something with a drier, firmer touch. Not only that, but I also hope that this textile culture, which is so closely connected to the land where it was created, continues for a long time even if for one more day."
Tomihisa tells us that he enjoys this cooperative work too: "As a craftsman, it's really intriguing to take on something you've never attempted before." By refusing to stay still and by using the knowledge and techniques that have been refined over the years, it becomes possible even now, little by little to innovate a culture that is steeped in history.
Text: Kosuke Ide
Photo, Movie: Keisuke Fukamizu
Movie edit: cubism
2023.1.10 Republished with revisions
2022.5.24 Original work published